Daniel Heinze: Working toward faster, stronger, and more efficient 3D printing
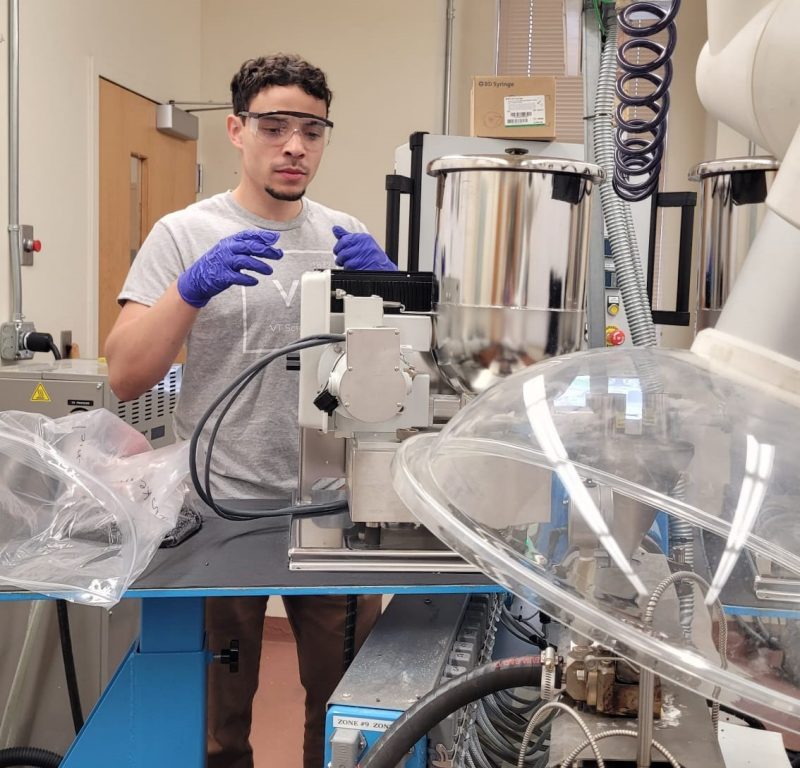
This story was written in the spring of 2024 by GRAD 5144 (Communicating Science) student Katie Tiller as part of an assignment to interview a classmate and write a news story about his research.
3D printing, or additive manufacturing, has taken the world by storm, and its applications have expanded into every industry and sector. This process allows us to create a three-dimensional (3D) object from a digital model, opening up a world of possibilities for the creation of items from prototypes to parts to foods and even to new organs.
Although 3D printing technology has become increasingly popular, the actual physics of the materials involved has eluded scientists for decades. We know 3D printing works, but we don’t necessarily know how it works. Daniel Heinze, a third-year Ph.D. student in the Macromolecular Science and Engineering Program at Virginia Tech, is investigating the materials used in 3D printing to try to develop materials that allow for faster, more efficient, and stronger 3D printing.
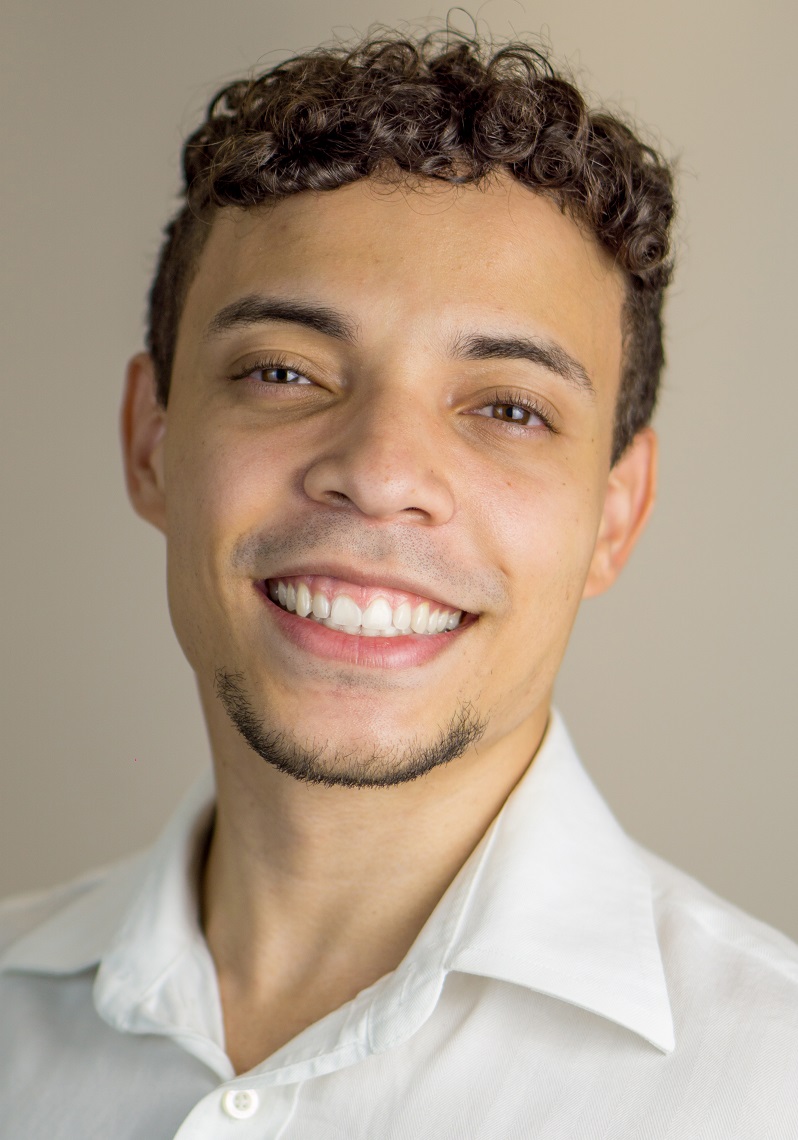
Heinze’s interest in materials began after he graduated from high school while he was working in his home country of Brazil for a company that manufactures foams. This interest led him to obtain both a bachelor’s and a master’s degree from Federal University of ABC in São Paulo, Brazil, where his curiosity about materials developed further. He became interested in polymers, or plastics, and their composition and application. With a growing interest in working in the research and development of polymers, Heinze decided to pursue his Ph.D. at Virginia Tech.
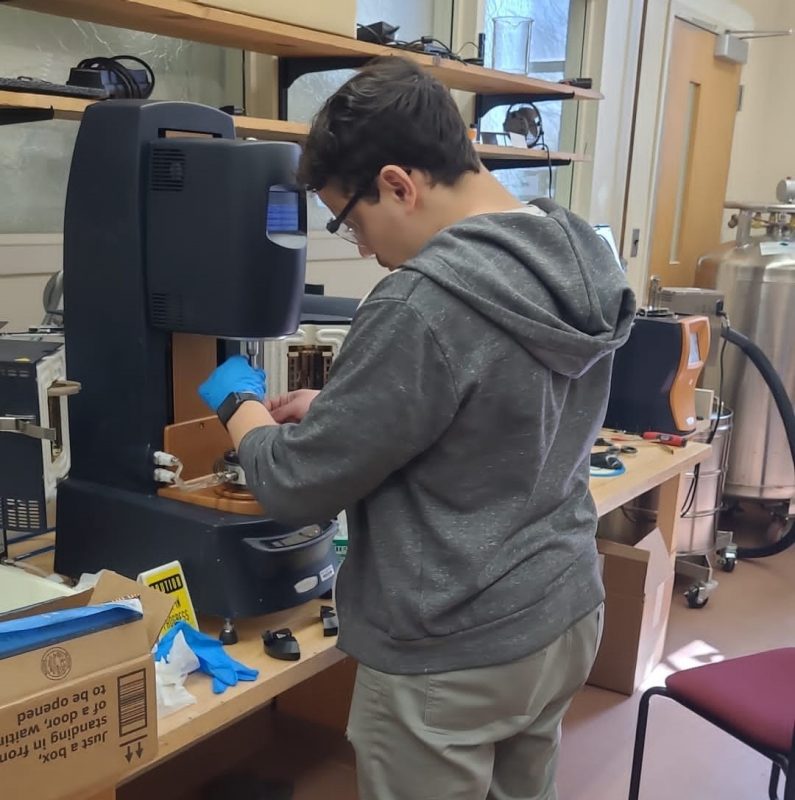
Heinze currently works with Medium Area Additive Manufacturing (MAAM) and is investigating the properties of the polymers being printed to increase printing speeds. Many people tackle the issue of slow printing speeds by tweaking the machines. Heinze, however, is focused on altering the composition and properties of the polymers being printed to increase printing speeds and reduce the number of defects present. To do this, Heinze alters the proportions and types of materials that go into the polymers to study both their thermal properties and flow, two characteristics of polymers that can drastically alter printing speed and the quality of the printed material.
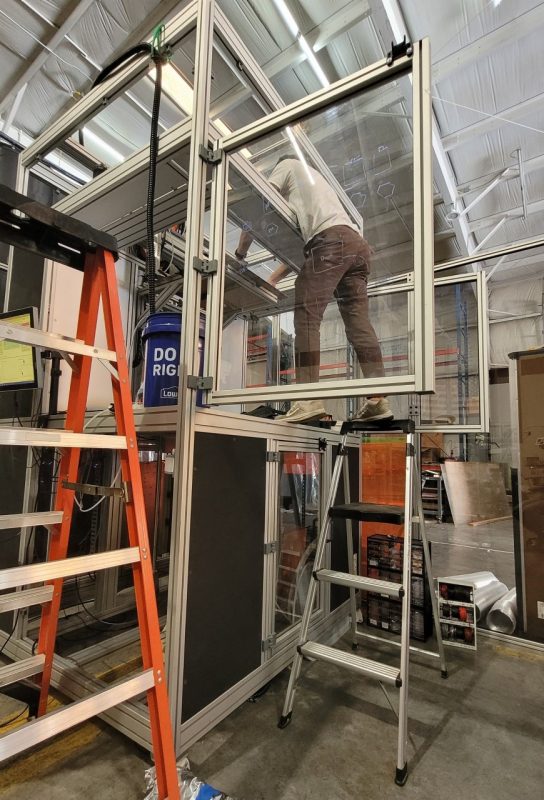
Once objects are printed with the new polymer composition, Heinze investigates the quality of the printed materials in a variety of different ways. He first compares a 3D scan of the printed part with the original file the object was printed from to identify any shape defects. He then investigates the rheology, or the flow of the polymer from the 3D printing machine. He also performs thermal imaging and thermal analysis to investigate the temperature of the polymer as it is extruded and cools to ensure proper adherence of each layer that is printed. Lastly, Heinze performs a morphological analysis using scanning electron microscopy (SEM) to investigate the surface topography for a more in-depth structural analysis.
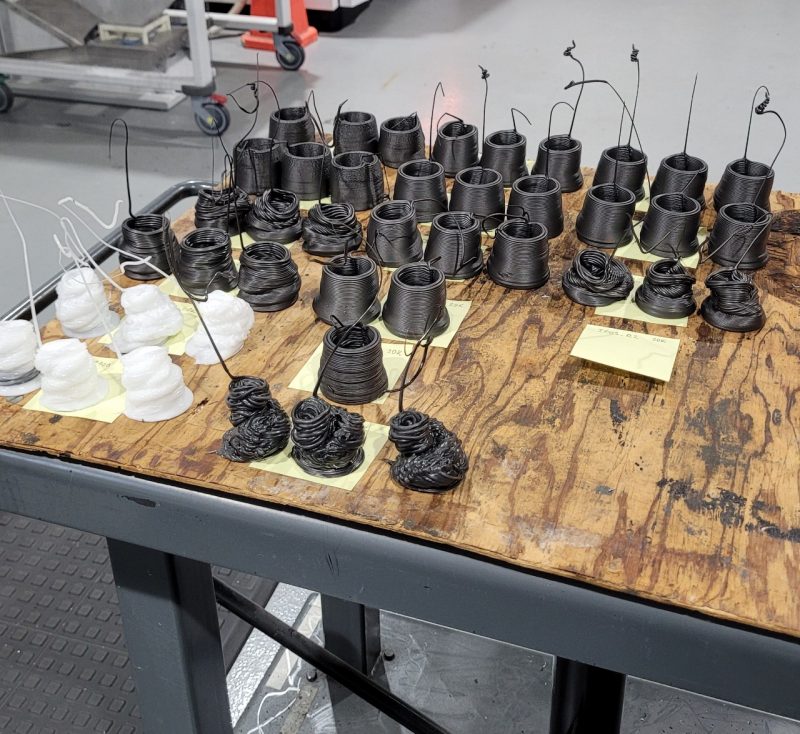
Overall, Heinze hopes his work will open many doors within the realm of 3D printing, leading to improvements and new additive manufacturing technologies that will be broadly applicable to many different industries. Identifying the optimal composition of polymers for MAAM 3D printing will allow for faster printing and stronger and higher quality printed materials. It will also generate less waste via the production of an unlimited number of parts or items without the need to create molds. Heinze’s work with polymers is helping to usher in the next era of 3D printing technologies.