Joseph Brooks: Designing airplane improvements to fly toward a better future
This story was written in the spring of 2021 by GRAD 5144 (Communicating Science) student Zerin Mahzabin Khan as part of an assignment to interview a classmate and write a news story about his research.
The coronavirus pandemic has hindered most international air travel. We’ve had to hunker down and be content with simply dreaming about the day we can travel across borders again, the wisps of clouds close enough to touch and the crisscrossing roads of our cities blurring with every mile the airplane surges.
What if traveling by airplane could be even better than it was before the pandemic? What if airplanes could become lighter, and we could therefore fly farther, faster, and at cheaper rates?
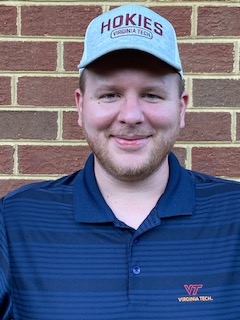
Joseph Brooks, a fourth-year doctoral student in Virginia Tech’s Department of Aerospace and Ocean Engineering, is developing a method to turn this dream into a very tangible reality. Aircrafts need antennas for many things, including communication and detecting weather patterns. However, current designs may have a large dish mounted in the nose of the aircraft, which is impractical for small planes. Alternatively, an antenna can also be placed on the airplane’s exterior either on the top or bottom of the main body or wings, which can interfere with the aerodynamics.
Brooks is addressing this problem by incorporating the antennas into the very skin of the aircraft to remove the need for extra, unnecessary space and weight. He is specifically researching the optimal design and materials for the antenna by using a combination of copper, fiber glass, and carbon fiber to create designs that will replace the current systems. This optimization does come with a caveat, since using stronger materials make the aircraft heavier. On the other hand, lighter materials can cause the airplane to become weaker. In addition to developing prototypes, Brooks also uses computational and mathematical modeling to iterate through his designs and strike a balance between the material’s strength and weight, while simultaneously considering the mechanical stresses that are important during flight.
Brooks can trace the trajectory of his passion for his project all the way back to his childhood, when he grew up in a rural part of Virginia. He liked working on equipment and was fascinated by both mechanical engineering and airplanes. He found his calling when he heard about the aerospace engineering program at Virginia Tech, which could merge his two biggest passions together.
“I enjoyed tinkering with things when I was young,” Brooks recalls. “I guess I can blame where I ended up now on playing with Legos!”
Brooks has always loved doing the most with the least by increasing efficiency, the very heart of what it means to be an engineering student. He is fascinated by the research in his project, although it does come with its own set of unique challenges. For example, on top of the importance of mechanical stresses on the structural form of airplanes, it is also necessary to consider and balance the electromagnetic effects during flight. However, instead of letting these issues deter him, Brooks enjoys working within the constraints to satisfy all requirements.
“I had no previous exposure to aircraft antennas or how they work, but this project has really helped me learn the basics, including design,” he comments.
Brooks became interested in this project during his senior year of undergraduate studies, when he conducted research for extra credit hours. He built off of a graduating student’s project when he realized the potential of this work and the impact it could have on improving air travel.
The results so far look promising, as Brooks’ models show the designs can support up to 160 kilo Newtons of load without buckling, while only having masses between 0.06 and 0.16 kilograms—relatively light in the world of aircraft design, according to Brooks. Essentially, this design will enable the aircraft to withstand mechanical loads 9 times higher than its actual flight loads.
Once Brooks finishes these optimization studies, he can begin testing the designs and materials on different aircraft models. Integrating the antennas more efficiently into the airplane will enable engineers to use the empty space where the original antenna used to be. As a result, these lighter and improved aircrafts will hopefully not only decrease manufacturing costs, but also enable extra functionality. For example, smaller aircrafts can be integrated with more sensors, allowing these airplanes to obtain during flights more direct radar information that would have previously only been available to traffic control towers.
Perhaps someday in the future, thanks to engineers like Brooks, safer flights can become the new normal!